Maths, Physics & Chemistry
Non-cuttable material inspired by seashells
We created the first non-cuttable material by mimicking the unique shell structures of the abalone sea creature. The material dynamically interacts with cutting tools turning their own energy back against them. Such hierarchical material systems, akin to natural organisms, but made of metal, ceramics and high-performance fibers, could provide a rich array of material technologies for the future.
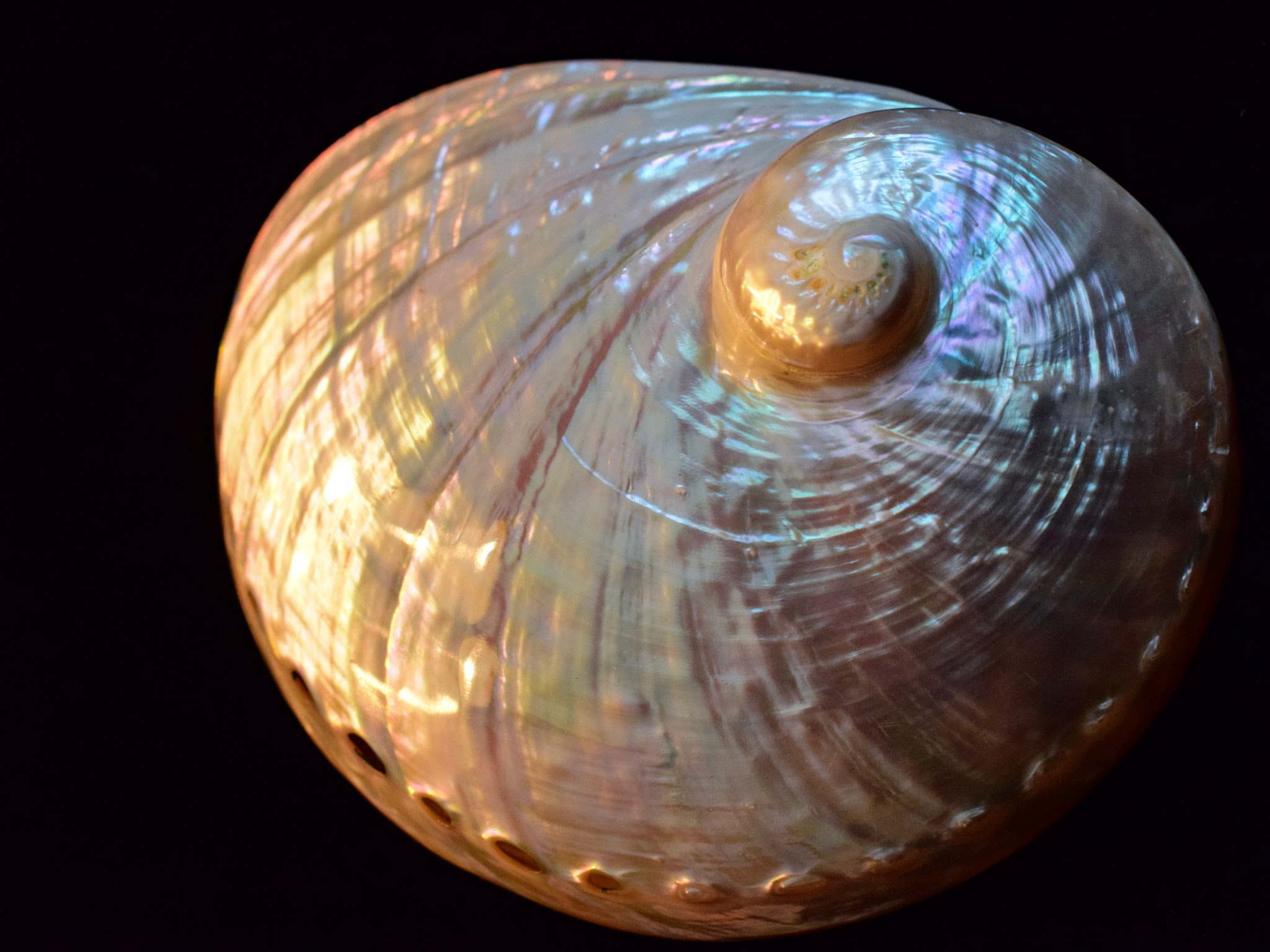
Nature is dynamic and complex. Therefore, creatures generate the most efficiently functioning biological materials. For example, abalone sea creatures have shells that resist attacks by predators to crack them open. Shells combine hard calcium carbonate crystals interleaved with softer layers of viscoelastic proteins. The interlinking of hard tiles in the softer material maximizes their resistance to cracking while keeping them light. Human-made materials usually achieve hardness just using a single material, such as metals or ceramics which are typically heavier and more rigid and often more brittle. Instead, we created a non-cuttable composite material, namely Proteus, which has a similar structure to the abalone sea shells.
The manufacturing of Proteus is similar to baking a loaf of bread: we mix metallic powder with a foaming agent that causes it to rise, later during the heating. Then, we insert ceramic spheres in carefully selected locations in the mixture and bake it in a furnace. The spheres are like hard nuts floating in the softer more spongy material. Next, we rapidly cool the baked material. Finally, we end up with Proteus. We named the material after the shapeshifting god in Greek mythology, because it dynamically evolves in response to attacks.
We used a special type of ceramic made of weakly consolidated ceramic grains because this produces an abrasive, sandpaper-like interface, which grinds the cutting disc. Proteus also makes use of the dynamic of the attack tools through the strain rate effect. The strain rate effect means the resistance of the ceramic particles increases as the speed of loading gets faster. In other words, the faster the cutting tools attack, the harder the interface becomes. An angle grinder that took only 45 seconds to cut through steel armour was ineffective against Proteus.
We also made use of the vibrations and dynamics of fast-moving tools to enhance the resistance to cutting. We aimed to increase the vibrations of cutting tools such as angle grinder discs. Usually, natural disc vibrations produce waves travelling around the disc. When trying to cut Proteus, the rotating discs will hit a ceramic sphere which will induce more volatile vibrations in the disc by interacting with its natural vibrations. If there is an obstacle, it acts like a wave breaker, which results in more local vibrations and oscillations. They disrupt the cutting tool, as the material 'kicks back' against the cutting disc. In effect, the material uses the disc's own force, energy, and speed against it such that much of the cutting energy is turned back on the angle grinder. When a water jet is used to try to cut it, the spherical nature of the ceramic spheres lead to a different defense mechanism, widening the jet and slowing it down two orders of magnitude, and so also rendering the jet ineffective.
We combined the principles of physics, such as the vibrations and strain rate effect, with naturally evolved knowledge that is embedded in the living structures in the world around us. This suggests that bio-inspired structures with carefully selected spatial geometry and properties could outsmart conventional materials if we embrace systemic solutions that make use of dynamic material responses. In the short term, such bio-inspired materials could enable security solutions, such as bike locks and defensive doors, and non-cuttable protective clothing for factory workers or protective gear against accidental cutting. Furthermore, we envision in the future the development of a wide array of such adaptive material systems, inspired by the complexity and dynamic nature of biological materials, but made of metal, ceramics and high-performance fibers. The scientific knowledge embedded in processes and structures in our environments is a reminder of the value of the natural world, as well as the care and respect that we owe it.
Original Article:
Szyniszewski, S. et al. Non-cuttable material created through local resonance and strain rate effects. Sci. Rep. 10, 11539 (2020).
Next read: Creating the world’s fastest rotating object by Rene Reimann
Edited by:
Isa Ozdemir , Senior Scientific Editor
We thought you might like
More from Maths, Physics & Chemistry
Testing gravity through the distortion of time
Sep 20, 2024 in Maths, Physics & Chemistry | 3 min read by Sveva CastelloStacking molecular chips in multiple dimensions
Aug 30, 2024 in Maths, Physics & Chemistry | 3 min read by Lucía Gallego , Romain Jamagne , Michel RickhausReversible Anticoagulants: Inspired by Nature, Designed for Safety
Jun 12, 2024 in Maths, Physics & Chemistry | 4 min read by Millicent Dockerill , Nicolas WinssingerDistance-preserving moves always keep a point fixed
May 18, 2024 in Maths, Physics & Chemistry | 4 min read by Shaula FiorelliA resonance triggers chemical reactions between the coldest molecules
Apr 5, 2024 in Maths, Physics & Chemistry | 3 min read by Juliana Park , Wonyl ChoiEditor's picks
Trending now
Popular topics