Maths, Physics & Chemistry
Plastic is fantastic, but recycling is no magic
When it comes to recycling, not all plastics are equal. While the world still struggles to manage recycling streams for simple plastics like PET, manufacturers have been developing increasingly complex plastic mixtures. Fortunately, new techniques like STRAP show great potential to solve more complex recycling issues.
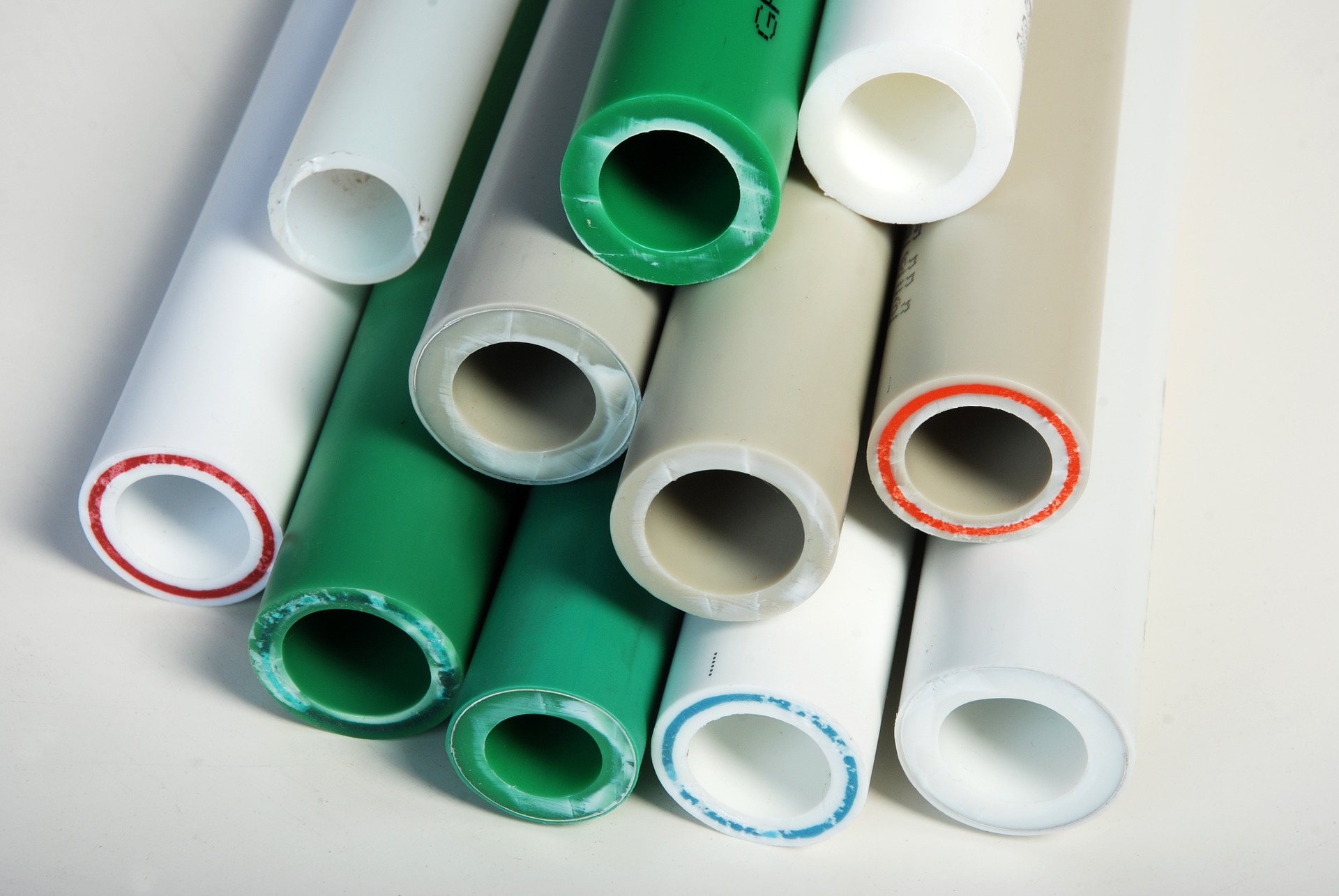
Plastic has been unbeaten for decades as the top packaging material. Plastic materials are lightweight, flexible and durable, and can easily undergo a plethora of recycling processes without being irreversibly damaged. Why then, do substantial amounts of unused plastic material end up going to waste?
Plastic is usually made up of a single chemical entity (a monomer) that is repeated to form a chain (a polymer). The chemical nature of the monomer will determine some of the features of the resulting plastic film, such as rigidness or transparency for example. It also determines which recycling procedure will be suitable.
While PET recycling is expanding across the globe to become the new norm for the consumer, industrials have developed new multi-layer polymer films, which are becoming increasingly difficult to recycle. In addition to that, inefficiencies in packaging production (such as cutting the film into templated shapes) lead to a lot of waste, which rarely gets recycled in the case of multi-layer films, despite not having been contaminated (with food for example). The problem with these multi-layer plastic films is that they require subsequent deconstruction of each layer into a pure material before being recyclable in conventional ways.
Meanwhile, research has advanced on that matter, Theodore Walker and colleagues from the University of Wisconsin-Madison have developed a strategy they call STRAP (standing for Solvent-targeted recovery and precipitation), which aims to separate the different components of a multi-layer film composed of PE (polyethylene), EVOH (ethylene vinyl alcohol) and PET (polyethylene terephthalate). Each of these components have their own function in the multi-layer film: PE serves as a moisture barrier, EVOH is an oxygen barrier and PET provides rigidness to the material.
Most of the plastics used can only be dissolved in some specific solvents. The idea proposed is to play with the differences in solubility of polymers, by choosing which solvent system is used and at which temperature, to dissolve only one of the three plastic components. This dissolved polymer is then filtered out while the two remaining layers are left as an undissolved solid. The dissolved plastic, now isolated, can be almost completely recovered and the solvents can also be reused. The study has shown that this process can be carried out with nearly 100% efficiency, meaning that almost all the initially used material can be reintroduced into the production chain. As a process that is not technically challenging, it could be implemented right at the source of the plastic waste streams. Closing the loop by feeding recycled material directly back into the industrial process would also avoid any pointless shipping costs.
For this process to be economically viable however, the price of the entire recycling process has to be lower than that of virgin plastic materials. In fact, recycled PET material from the STRAP-recycled film gets cheaper to produce than virgin PET material, as soon as the feed rate of a recycling plant exceeds 3800 tons per year. To put this into perspective, APK's Newcycling plant in Germany processes about 8000 tons a year, essentially making profit out of this recycling process and competing with producers of virgin PET material.
Limitations to this study however would be that conditions would have to be tailored to each type of multi-layer film. Other additives or adhesives that the films may contain can also make the deconstruction process of the plastic accordingly more difficult. Besides, this process is not presently adapted for post-consumption packaging waste as most of it is contaminated, for example with food. It nevertheless shows that there can be a financial incentive to consider recycling strategies as part of the development process for new complex plastic materials. Ultimately, if plastics aim to keep their monopoly in the packaging industry, environmental considerations will have to gain importance, when assessing the viability of a new material.
Original Article:
Walker, T. W. et al. Recycling of multilayer plastic packaging materials by solvent-targeted recovery and precipitation. Sci. Adv. 6, 1-10 (2020).
Edited by:
Dr. Beata Kusmider , Managing Editor
We thought you might like
Ocean acidification and its effects on coral reef growth
Jul 8, 2016 in Earth & Space | 3.5 min read by Rebecca AlbrightResetting nature’s clock: shifting seasons and species relationships
Sep 14, 2016 in Earth & Space | 3.5 min read by Stephen Thackeray , Sarah BurtheThe silent battle of young corals against ocean acidification
Oct 19, 2016 in Earth & Space | 4 min read by Taryn FosterFor polar bears the cost of living is rising
Mar 13, 2018 in Earth & Space | 4 min read by George DurnerMore from Maths, Physics & Chemistry
Testing gravity through the distortion of time
Sep 20, 2024 in Maths, Physics & Chemistry | 3 min read by Sveva CastelloStacking molecular chips in multiple dimensions
Aug 30, 2024 in Maths, Physics & Chemistry | 3 min read by Lucía Gallego , Romain Jamagne , Michel RickhausReversible Anticoagulants: Inspired by Nature, Designed for Safety
Jun 12, 2024 in Maths, Physics & Chemistry | 4 min read by Millicent Dockerill , Nicolas WinssingerDistance-preserving moves always keep a point fixed
May 18, 2024 in Maths, Physics & Chemistry | 4 min read by Shaula FiorelliA resonance triggers chemical reactions between the coldest molecules
Apr 5, 2024 in Maths, Physics & Chemistry | 3 min read by Juliana Park , Wonyl ChoiEditor's picks
Trending now
Popular topics